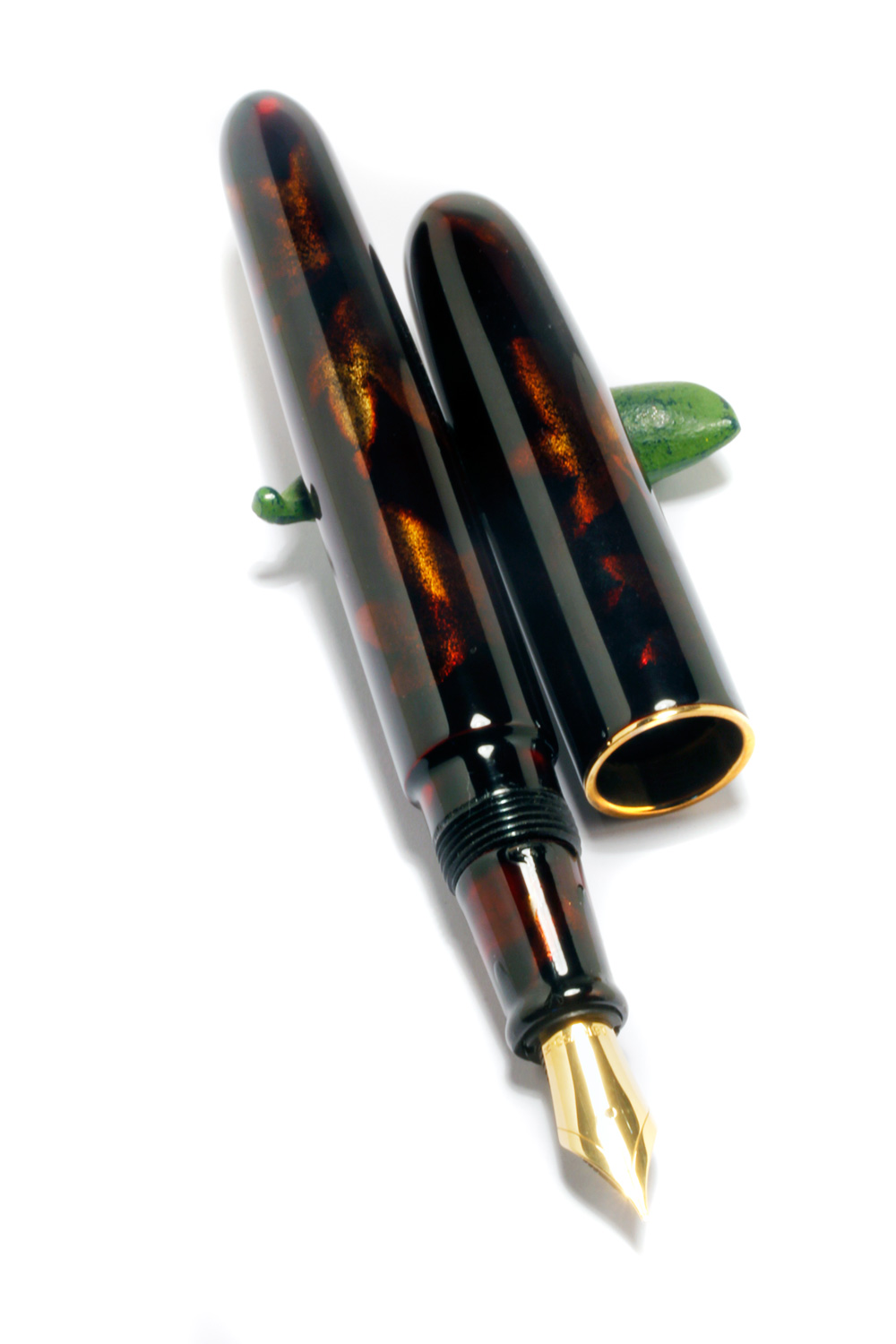
Urushi – Martin Pauli, the Master reveals the secrets!
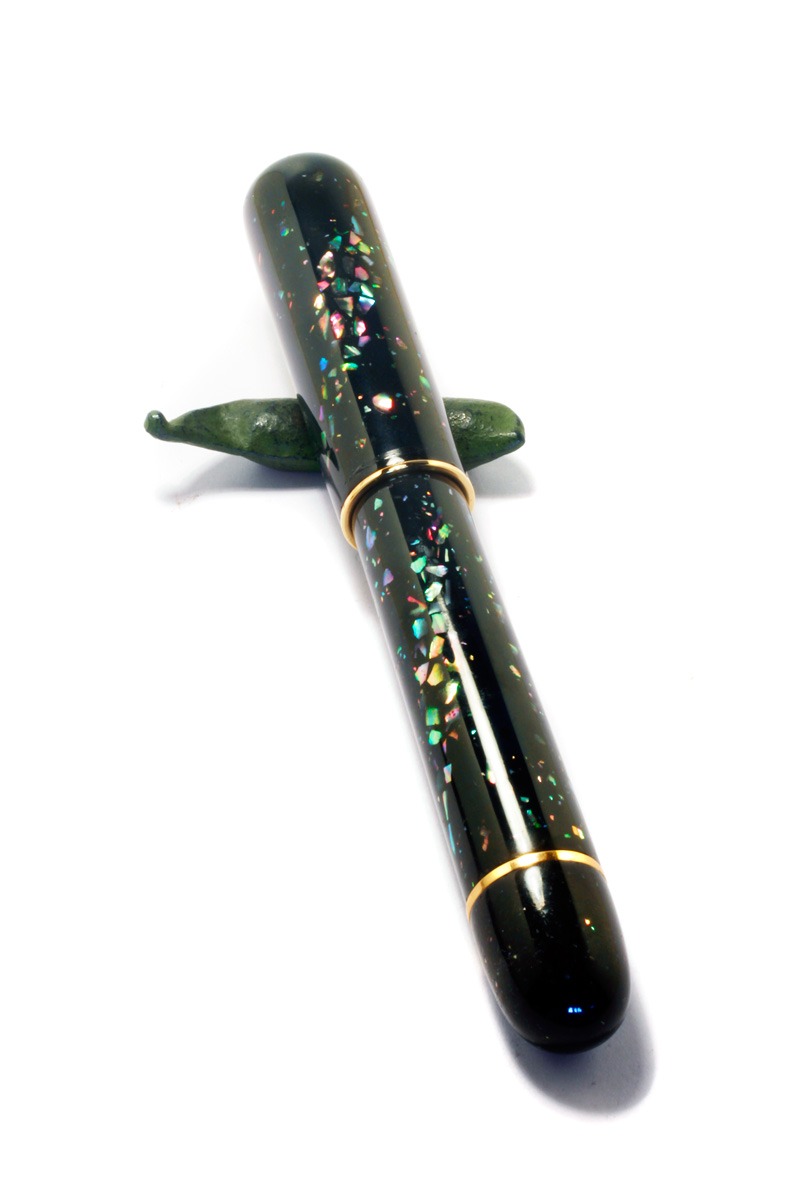
Urushi is a natural lacquer obtained from the lacquer tree (Reus Verniciflua). Similar to the rubber harvest, cuts are made in the bark of 7 to 10-year-old trees. The raw sap that runs out is collected, between 60 and 120 grams per tree. After the harvest the trees are leached out and felled. The harvest takes place between June and October, and the best quality is harvested in July and August.
In the liquid state, the raw lacquer is strongly allergenic. Once dried, this effect disappears and the lacquer has a strong antibacterial effect. This is why Urushi is used commonly in Japanese cuisine implements, such as chopsticks, soup bowls, plates and the likes.
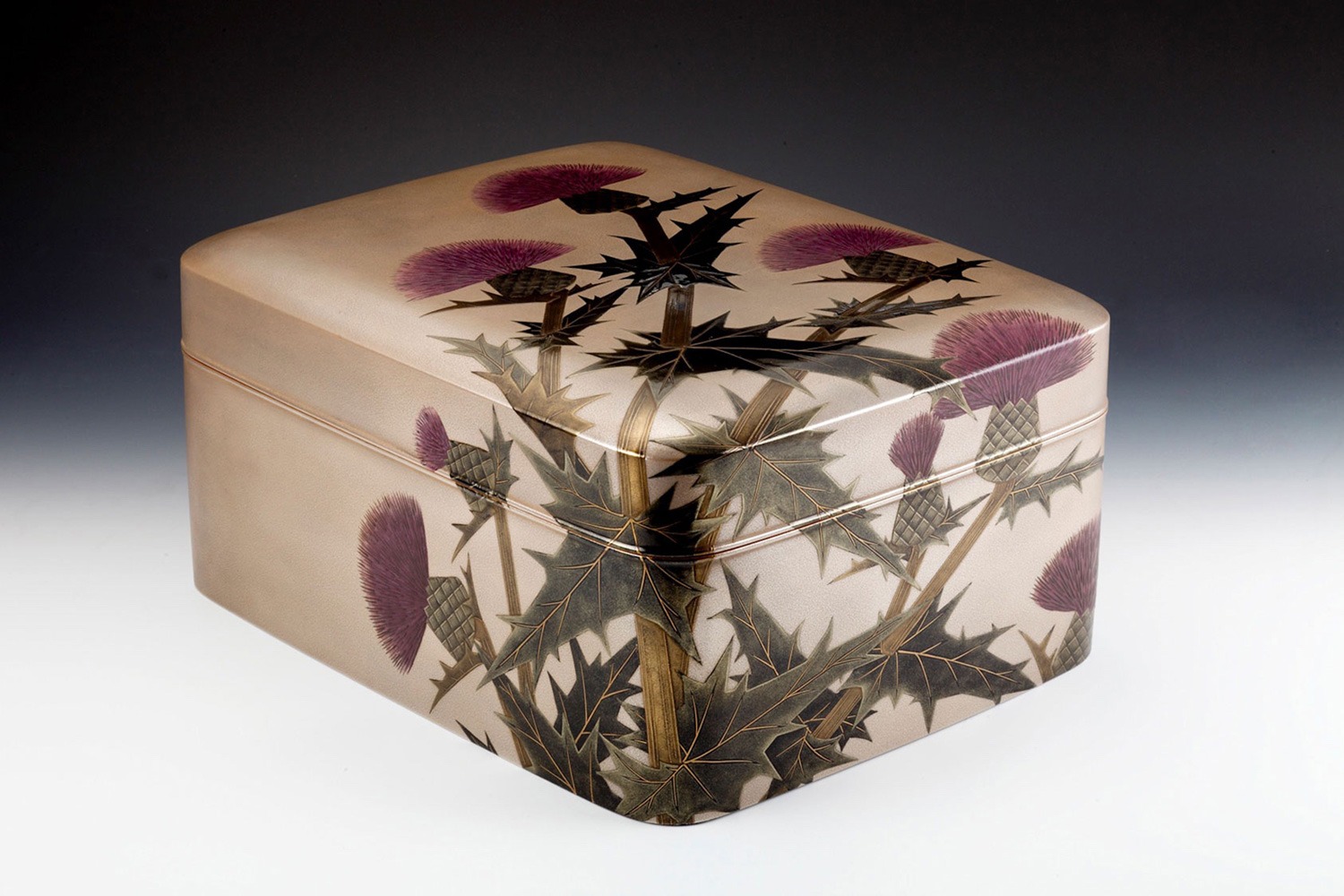
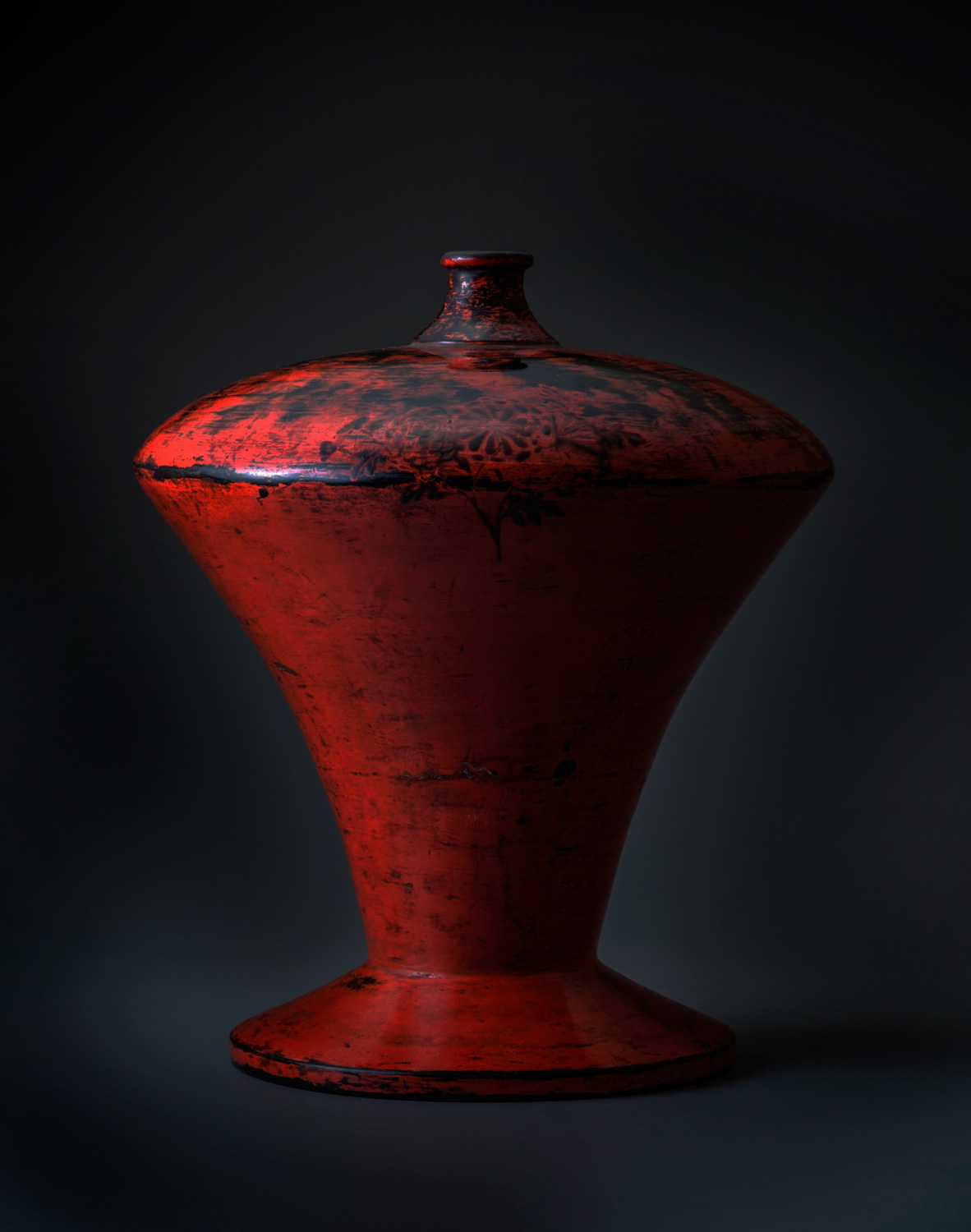
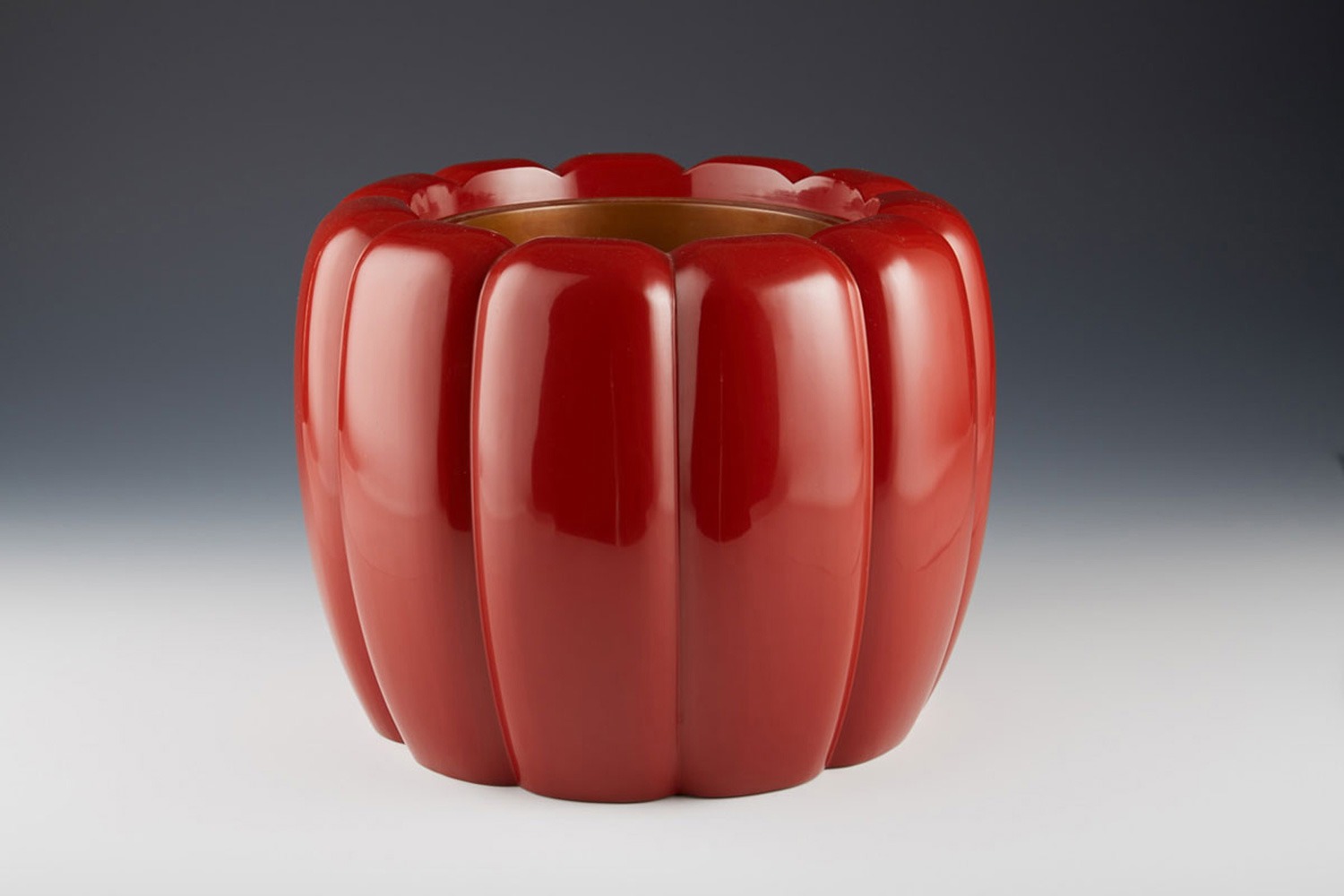
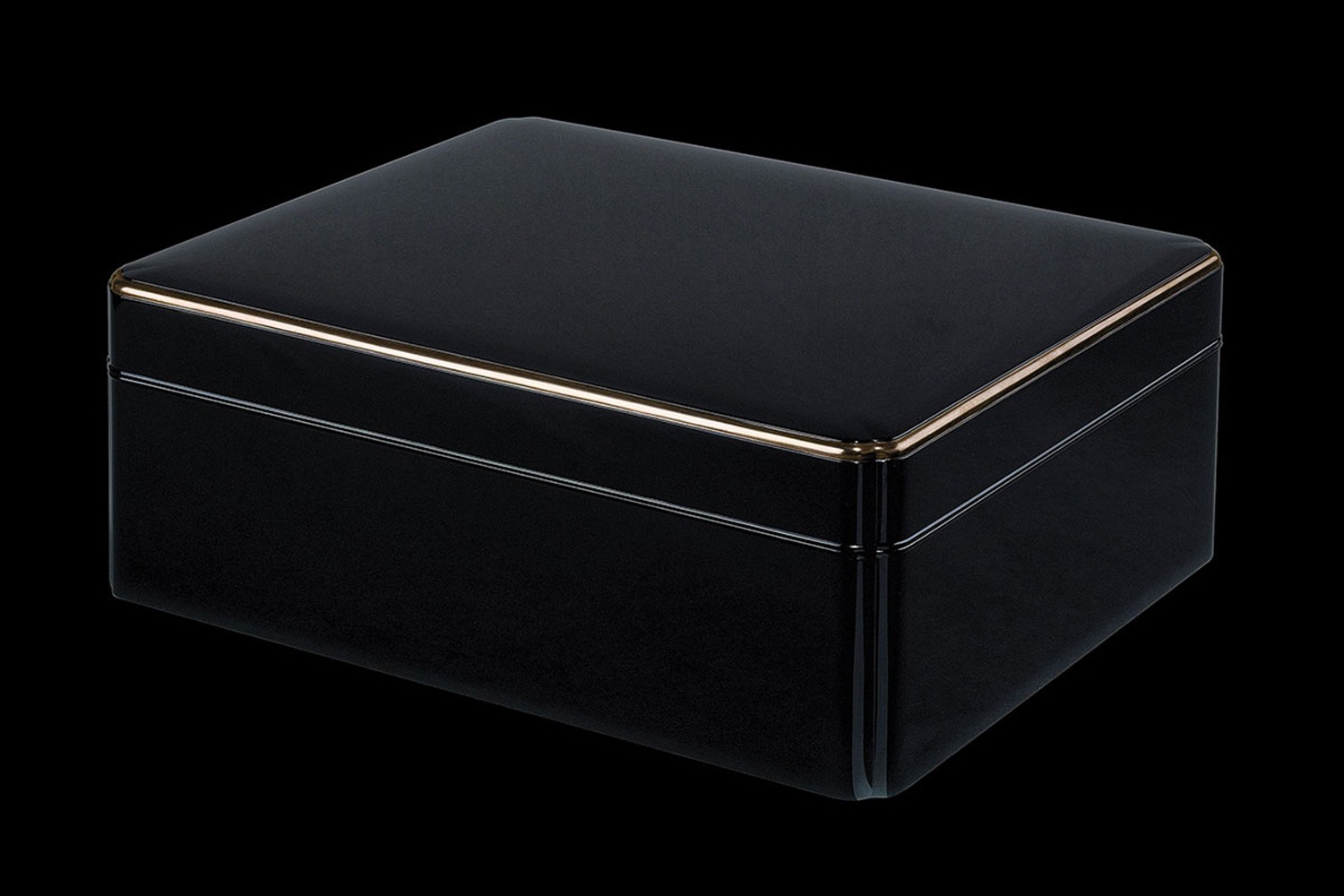
Durability/Quality
In Japan almost everything was refined, protected or decorated with Urushi, whether temple columns, palanquins, furniture, armor, weapons and household objects and much more. During excavations in Japan and China lacquer objects were found which survived 7000 years undamaged. In 1873, the Japanese government sent a collection of high-quality lacquer objects to the World Exhibition in Vienna. On the way back, the mail ship sank with its precious freight off the coasts of Japan. After 8 months the freight was salvaged. The specialists determined that the objects were in perfect condition.
Urushi is resistant to water, alcohol, all known acids and alkalis, and temperatures up to 300°C. UV light in the form of strong or constant sunlight can weaken Urushi.
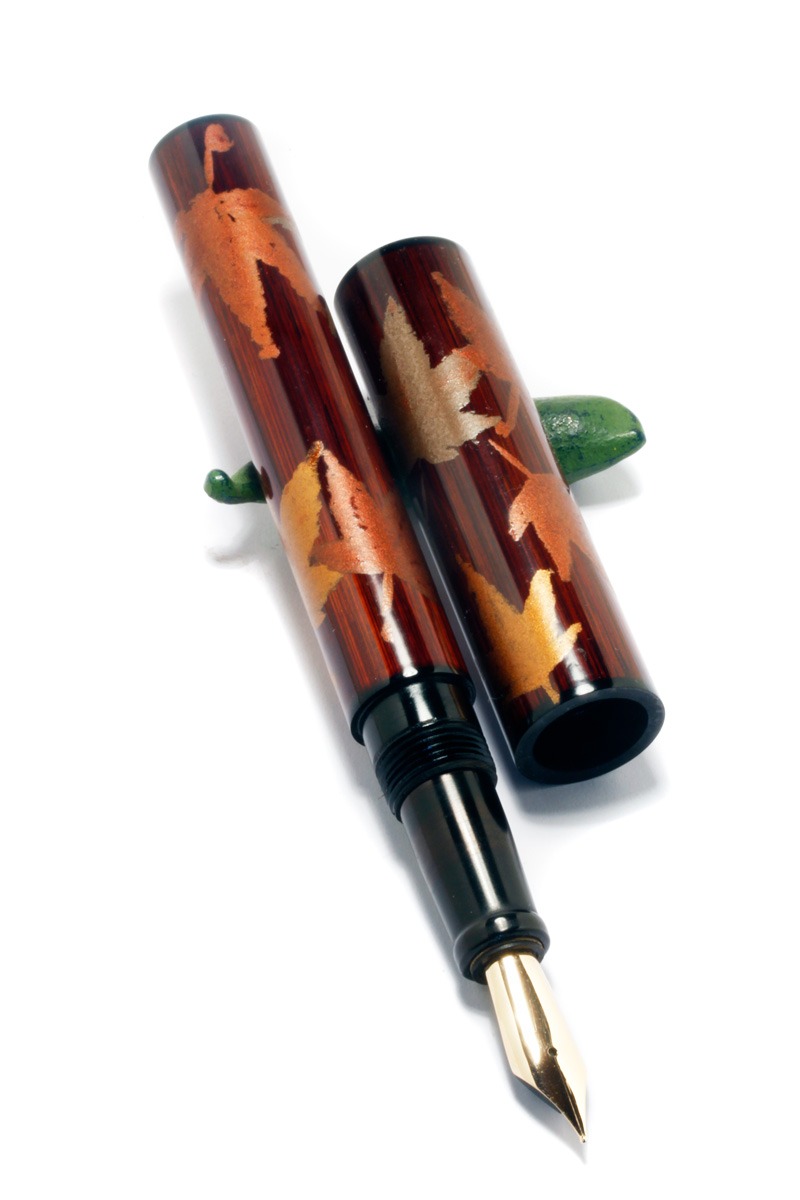
Urushi applied in thin layers reaches a solid hardness almost equivalent to glass.
Its medical effects have been studied and its use against parasites such as worms has been described. In northern Japan, its juice was part of a Buddhist practice for self-mummification “Sokushinbutsu” without posthumous interventions in the body.
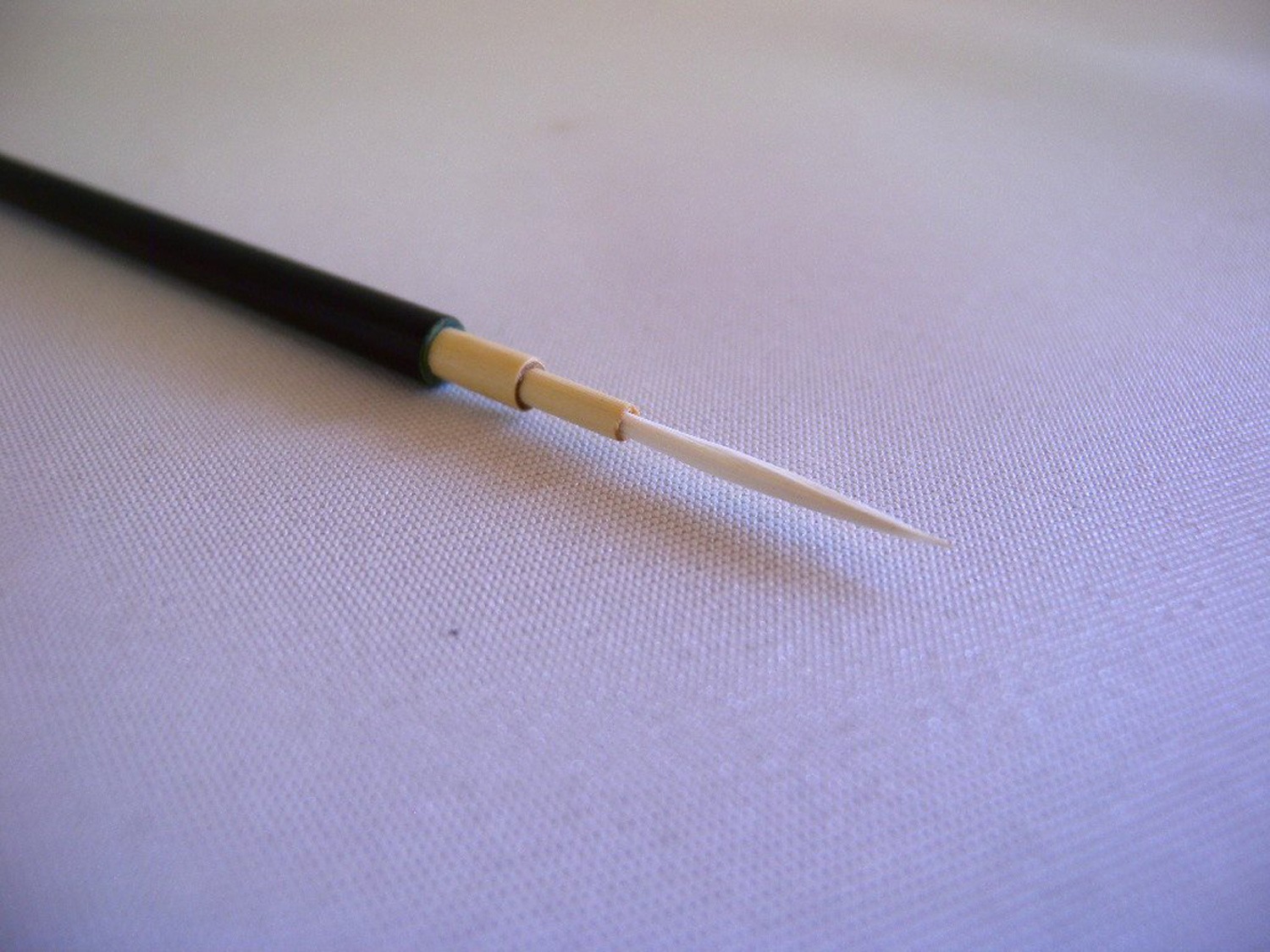
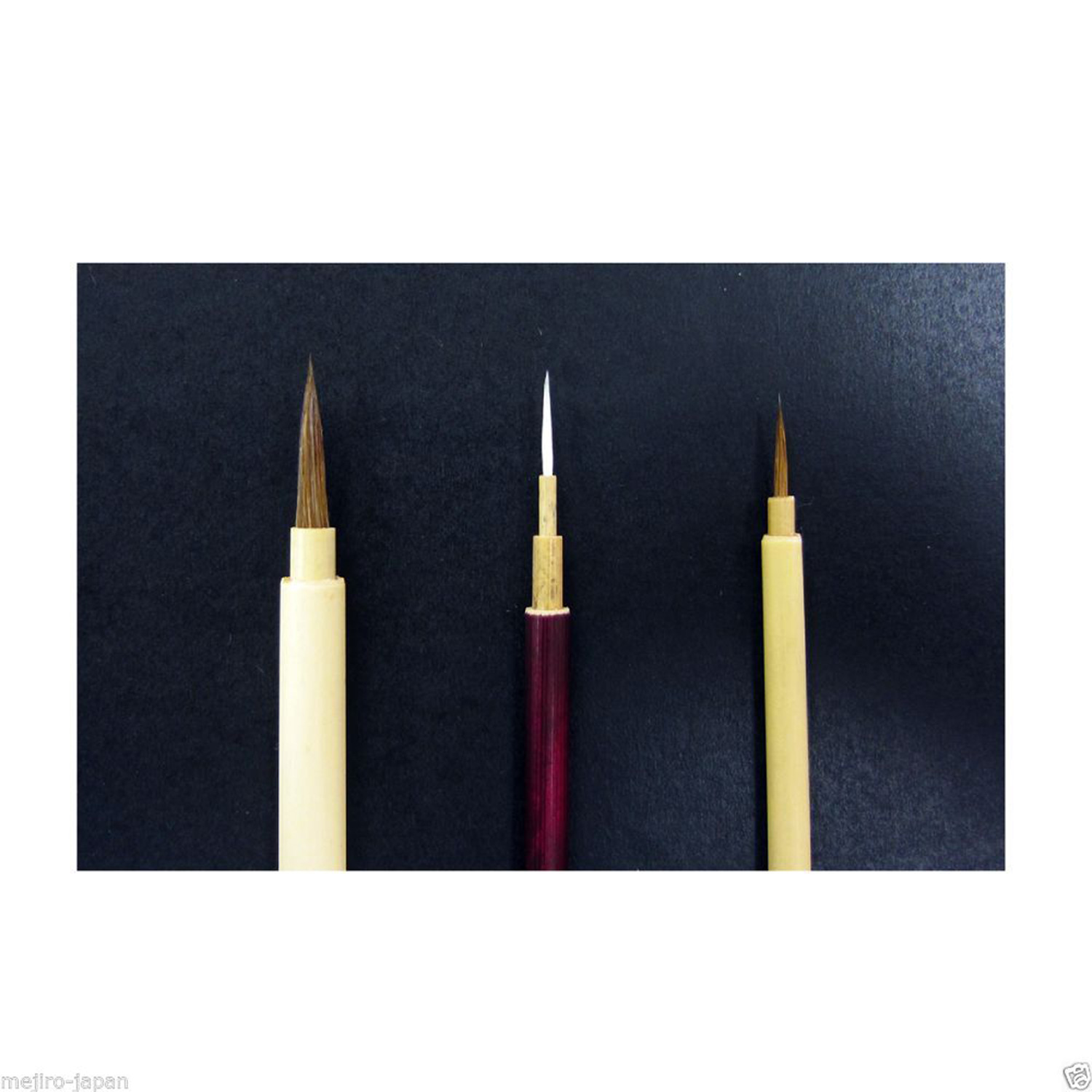

Tenbikurome – refinement of the raw varnish
The raw lacquer is called “Ki-Urushi” after filtering. In the spring sun a wooden tub is set up and Ki-Urushi is moved for hours with a squeegee. The varnish loses water and the sun causes a chemical process which makes the varnish darker and viscous. This process is called “Tenbi-Kurome” and the resulting high-quality varnish is called “Su-Kurome-Urushi” or “Sakari-Urushi”.
Sukurome-Urushi is used in its pure form or colored with pigments. The classic colors are red pigments “Bengara” (red iron oxide) and the black pigment pine carbon. Today, a large number of chemically produced pigments are also used.
Transparent black Urushi “Roiro-Urushi” is obtained by adding iron powder to raw lacquer. The iron produces a chemical reaction that colors the varnish black but still keep it transparent.
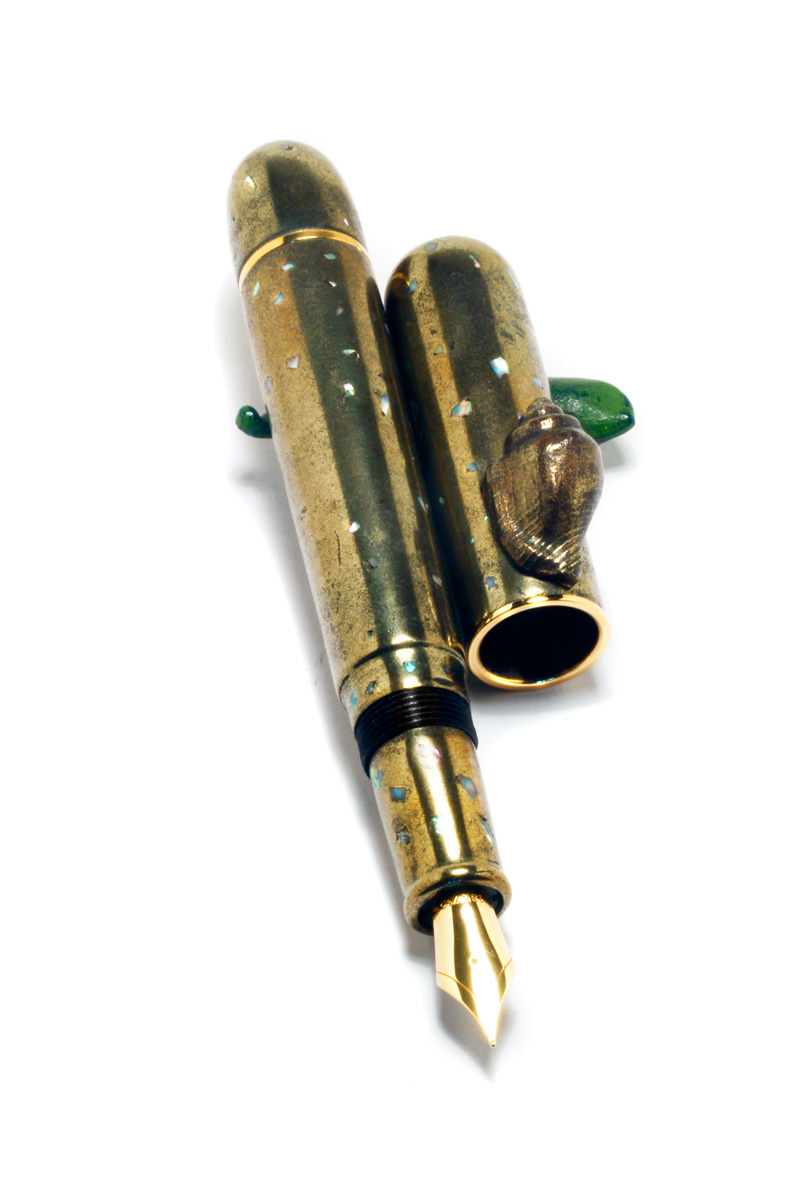
Processing
Ki-Urushi is used for various works, among others for the primer when building up a lacquer work. In wood processing, Ki-Urushi is used for coloring and sealing wooden surfaces. This technique is called “Fuki-Urushi”, Ki-Urushi is repeatedly rubbed into the wood surface, wiped off and hardened.
Urushi-Muro
Urushi does not dry at normal room temperature but requires high humidity.
For this purpose each lacquer craftsman possesses a damp cabinet “Urushi-Muro” traditionally built from softwood in which a constant humidity of 75% and temperature of ideally 25°C is maintained. A thin lacquer layer – often not thicker than 0.01 mm – hardens/cures/dries completely over 24 hours.
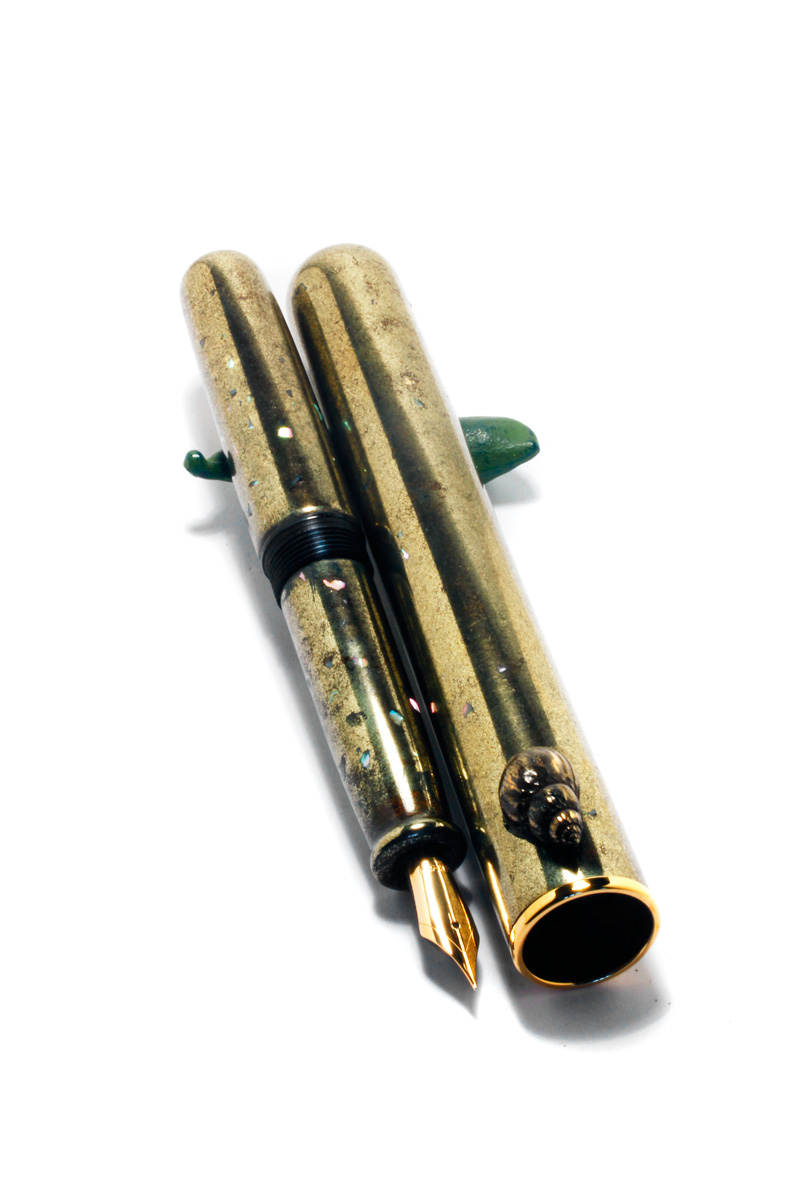
Tools
In this craft, various knives, spatulas, scattering tubes, the tooth of a fish for polishing small areas and much more are used. The most important tool is the Urushi Fude or Urushi Brush for driving the varnish made of women’s hair. Urushi is viscous and therefore the effect of the brush is more like a spatula than a classic brush. For fine work there are round brushes of various sizes, made from the hair of horses, goats, rats and other animals.
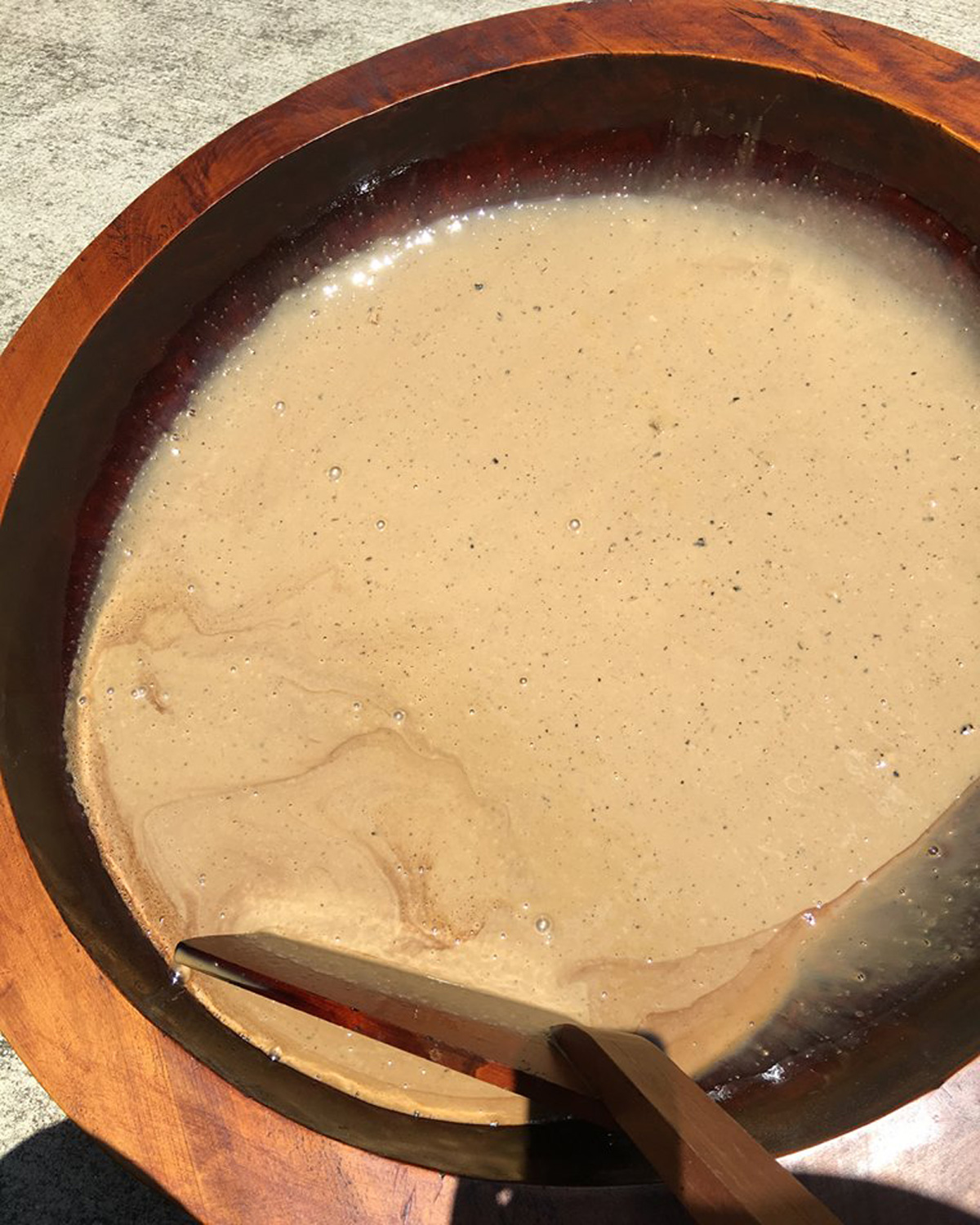
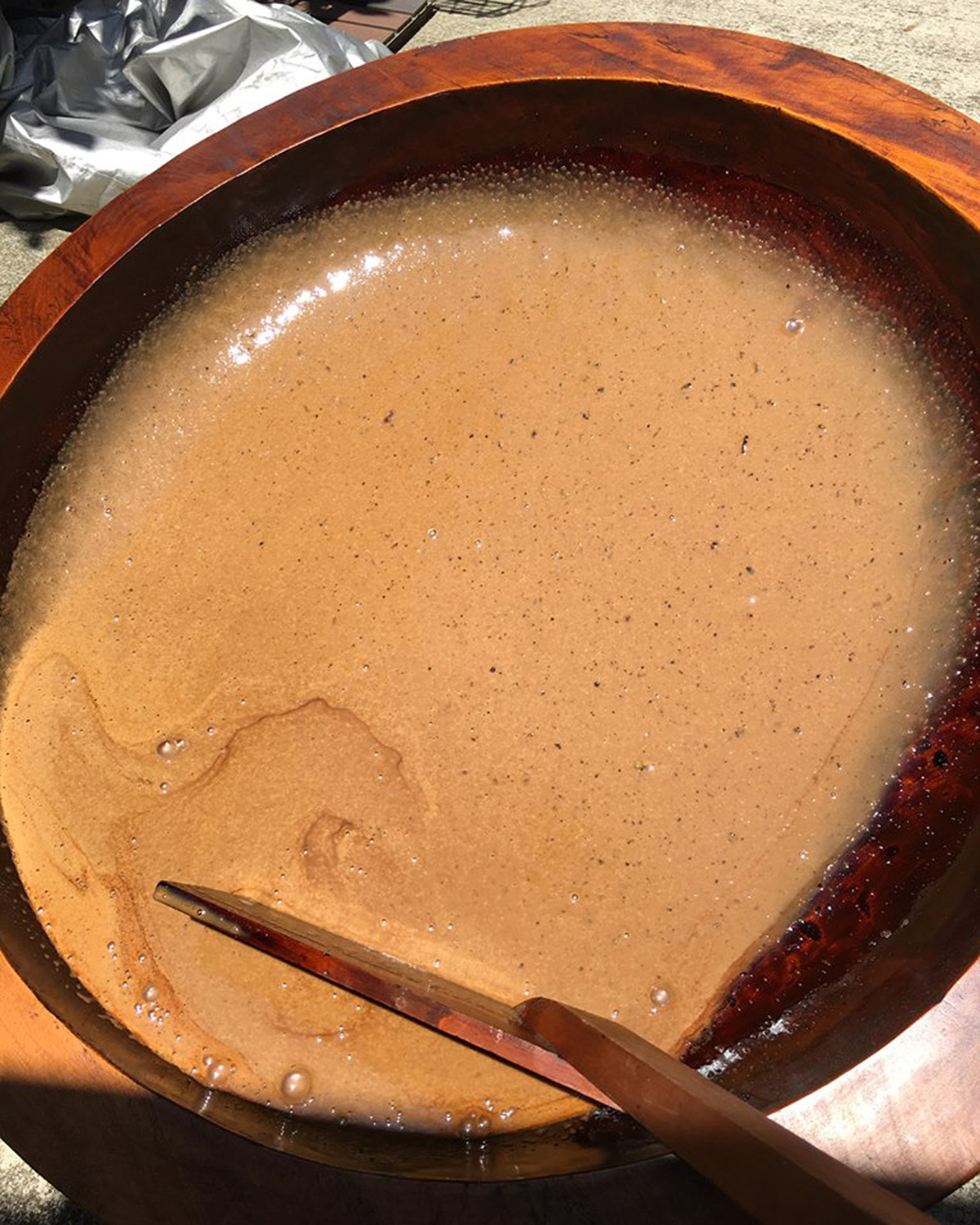
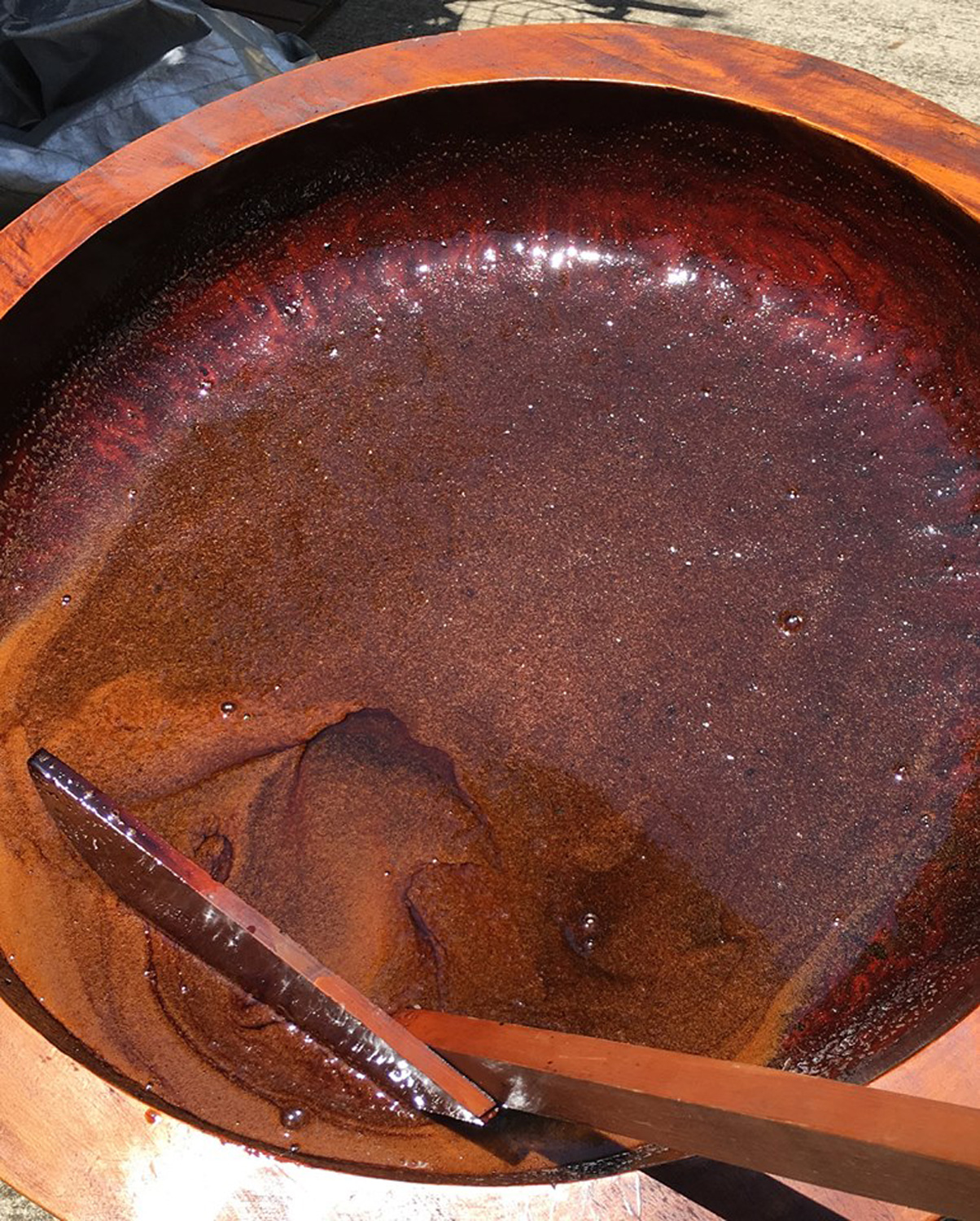
Urushi Techniques
Nuritate
Nuritate is a technique in which the last coat of paint is applied without polishing.
Roiro
Roiro-Nuri is the traditional, classic lacquer finish. In an elaborate “Uwazuri” process, the top coat is polished to achieve a mirror-like shine. The polishing process only takes 5 to 10 days. During polishing, the surface is finely sanded with charcoal. Then the varnish is pre-polished with cotton wool, rapeseed oil and a fine clay powder called “Tonoko”. The surface treated in this way is then rubbed with transparent Urushi, completely wiped with paper and hardened for 24 hours. This is repeated 5 to 6 times. Then the surface is polished with rapeseed oil, a fine polishing powder “Migako” and the fingertips.
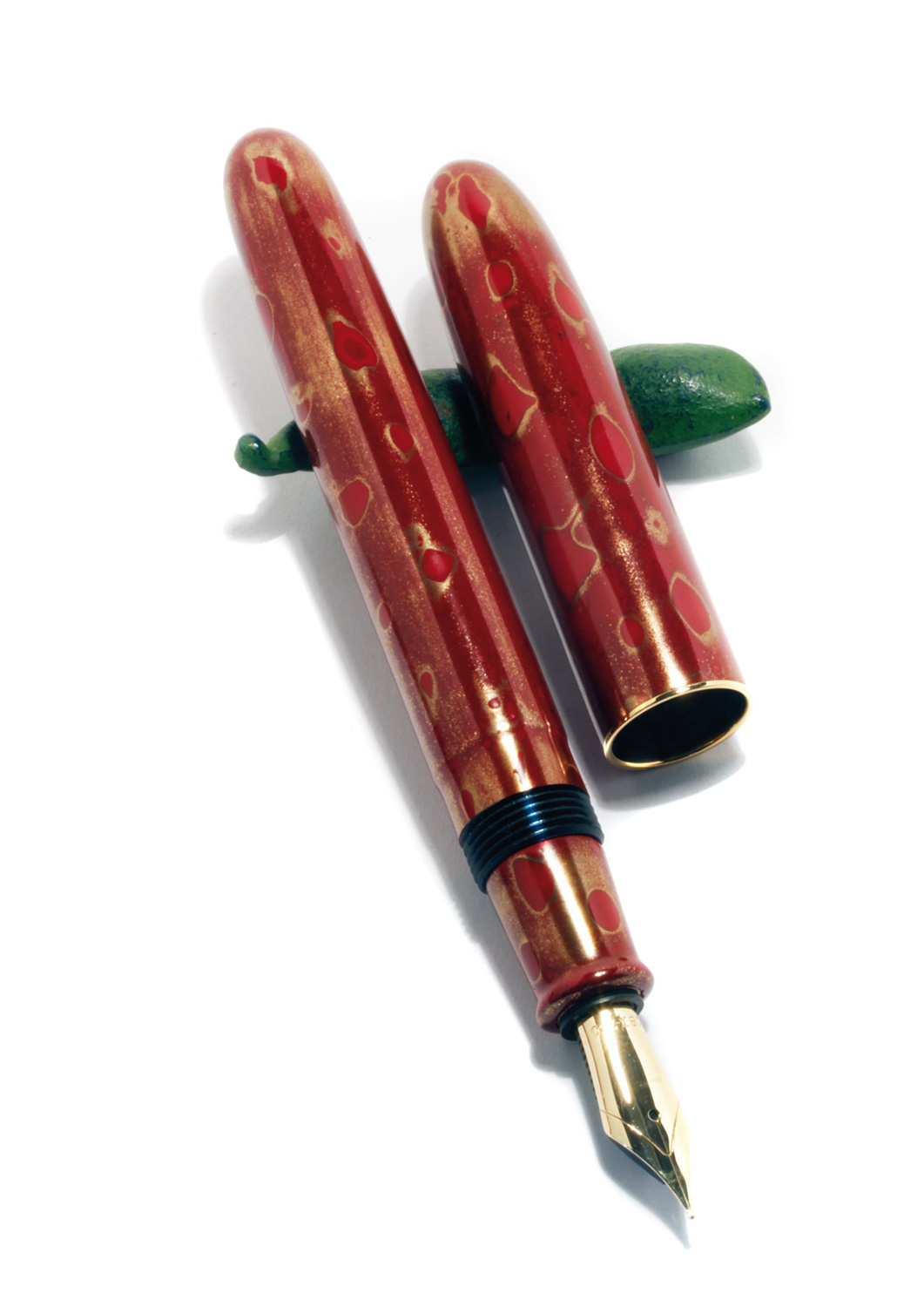
Maki-e
Maki-e means sprinkled pictures and is a technique in which flat and raised images are created by applying various metal powders and sheet metals to lacquer in complex work steps.
Tsuishû/Tsuikoku
A technique taken from China (Guri). Hundreds of layers of Urushi are applied, which are then carved and engraved. Depending on the size and thickness of the object, production can take years. “Tsui = carving, Shû = red lacquer, Koku = black lacquer”.
Negoro
Negoro-Nuri belong to a special group of lacquer. The name derives from a Buddhist temple complex, the Negoro-Ji in the prefecture of Wakayama. The temple was active from 1087 and was destroyed in 1585 during the turmoil of war that led to the unification of Japan under Ieyasu Tokugawa. In Negoro-ji all religious and profane objects were lacquered black and finished with a red top coat. After years of handling, the red topcoat gradually rubbed off and partially released the black lacquer underneath. This varnish represents the beauty ideal of “Yô no Bi” beauty through use.
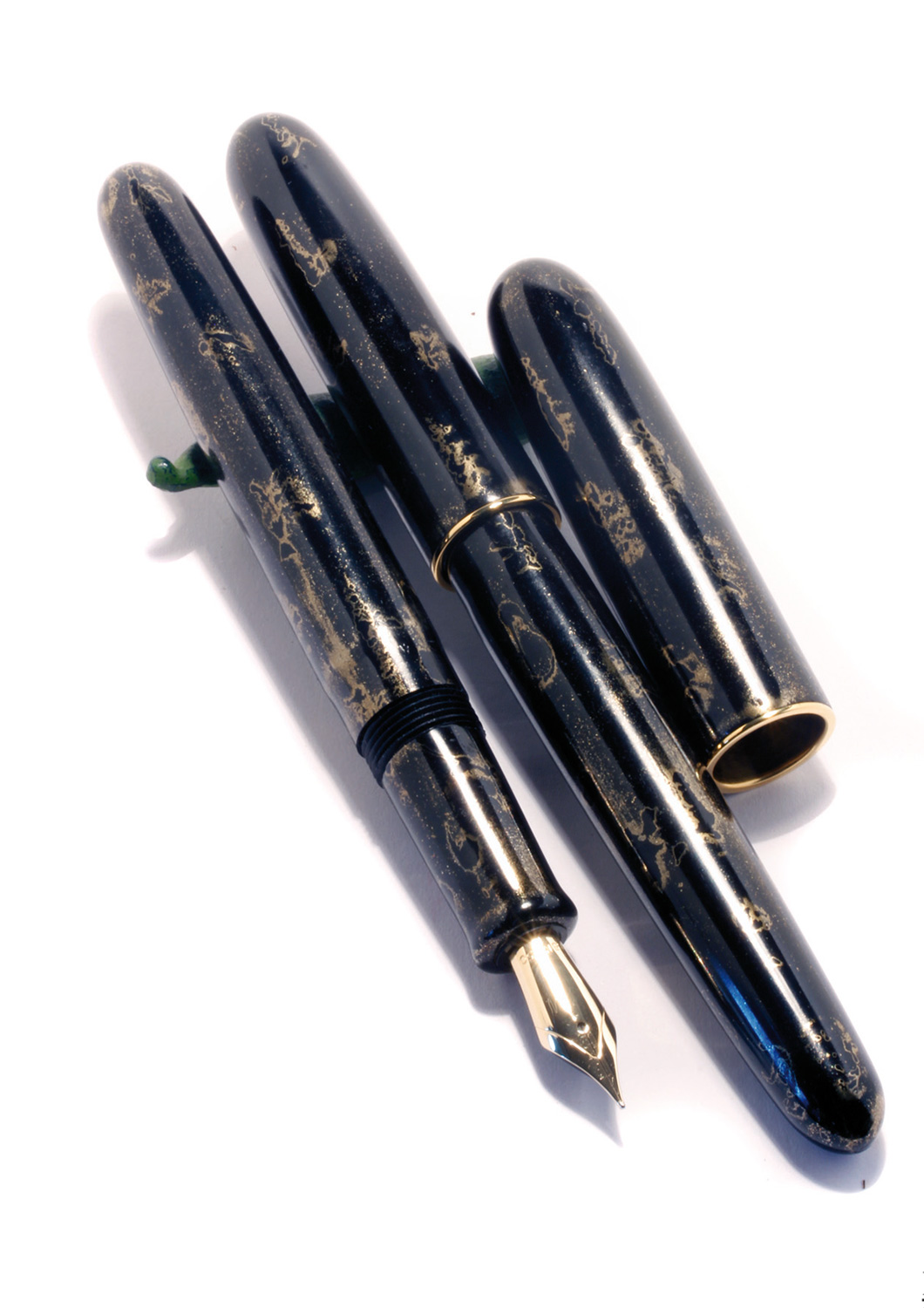
Kawari-Nuri – Experimental lacquer
Experimental lacquers “Kawari-nuri” or scabbard lacquers “Saya-Nuri” appeared in the early 17th century, when the government had imposed restrictions on the use of gold lacquers for the common people. At that time, the lacquer craftsmen (Urushi-Sei) began to experiment and combine lacquer with various materials and structures.
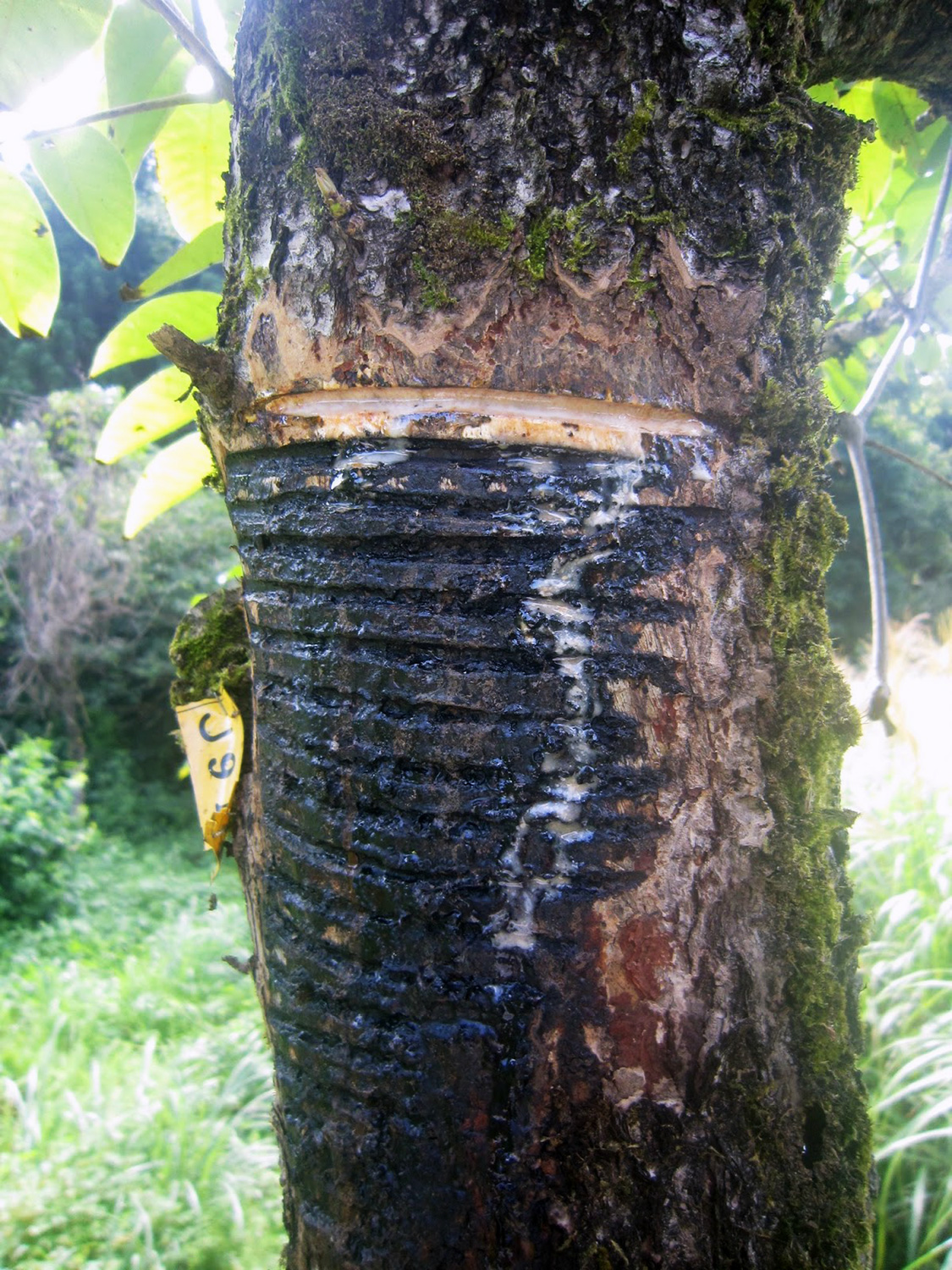
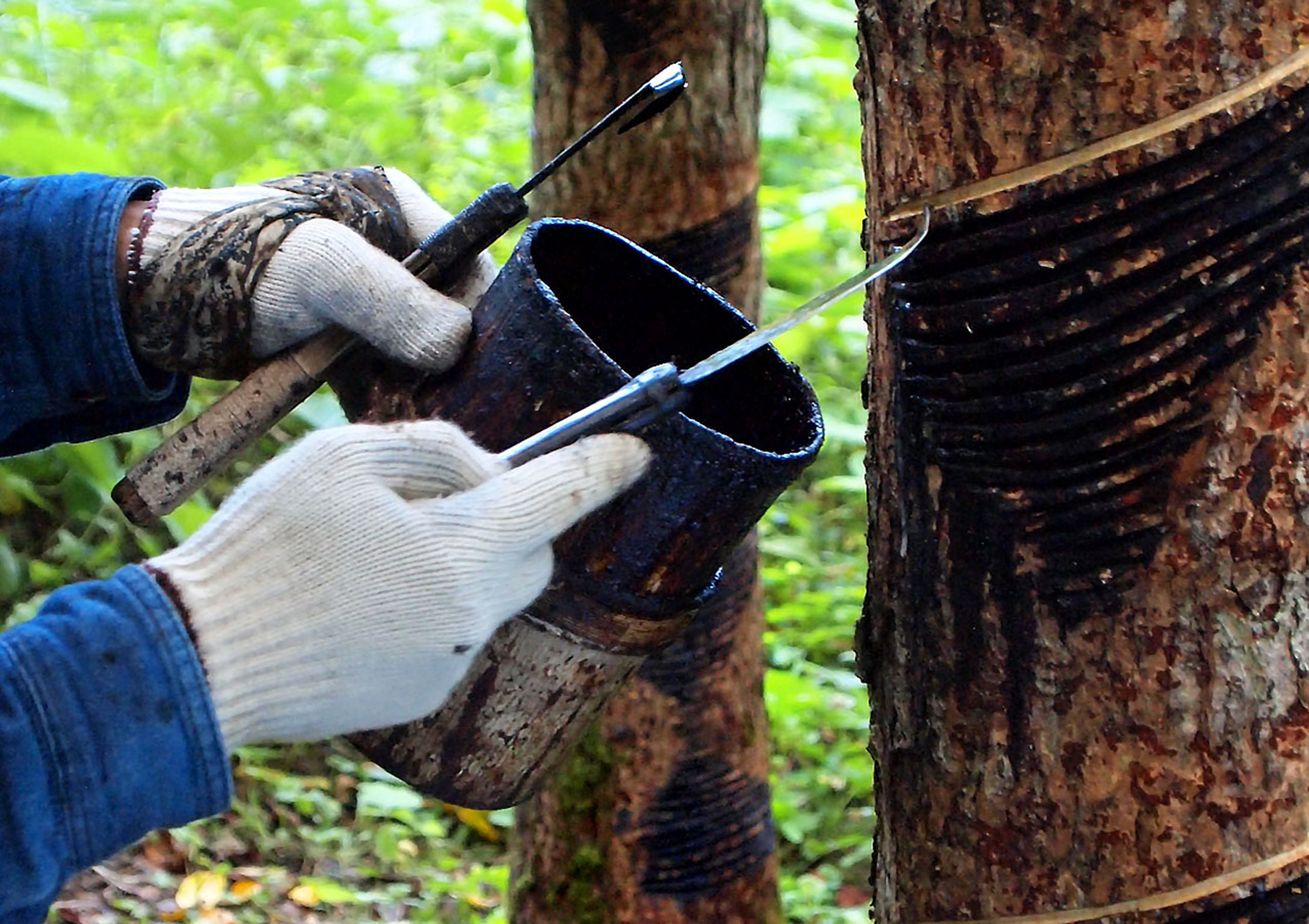
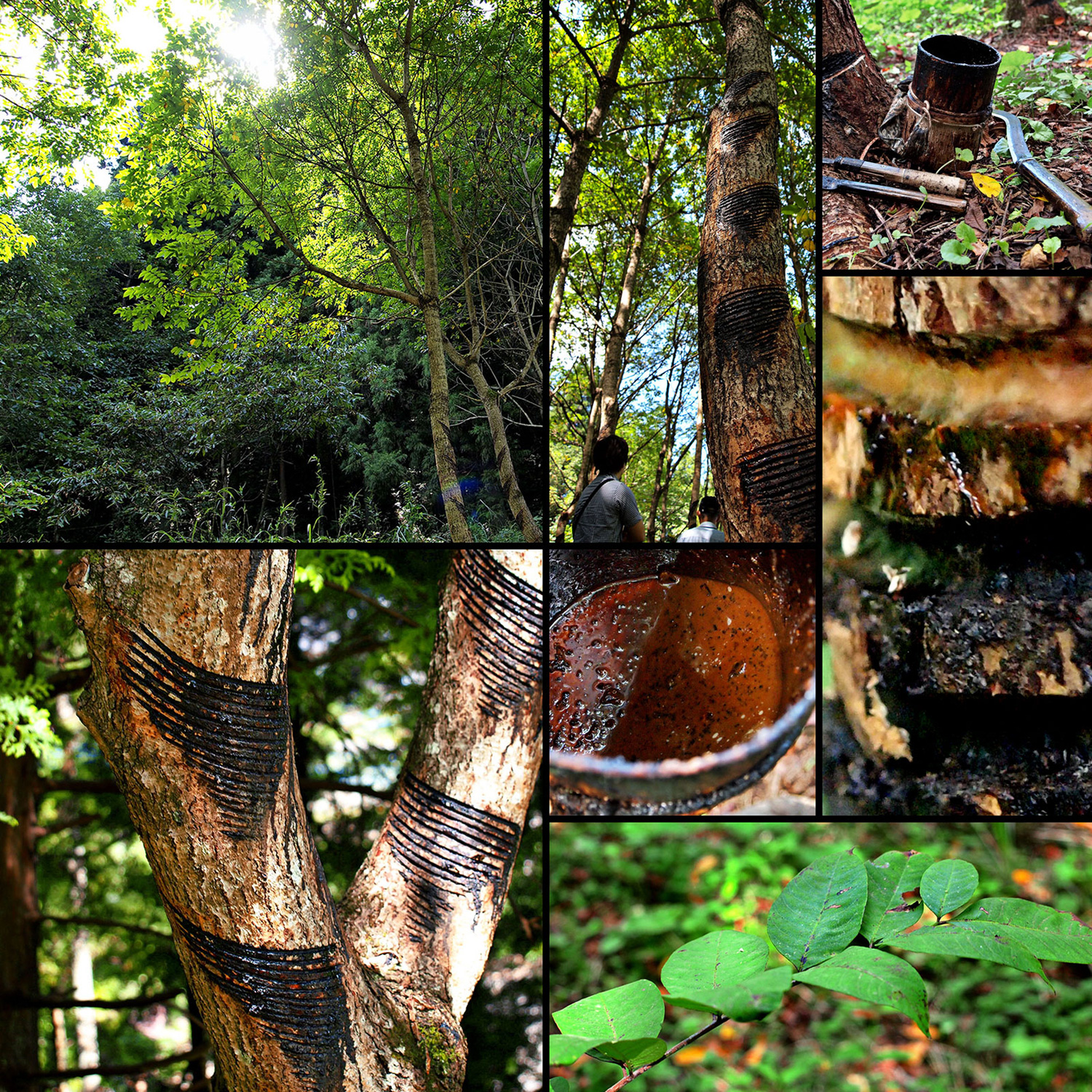
About Manu Propria
Very few people know that since 2013 there has also been a manufacturer in Switzerland that manufactures fountain pens with Urushi lacquer. Manu Propria (With own hand) produces handmade fountain pens, which are lacquered with Urushi in Switzerland. Manu Propria specializes in the reconstruction of old and development of new experimental lacquers. At present, customers can choose from over 100 different variants. The production of a lacquered fountain pen involves 30 to 100 layers of lacquer and takes 30 days to half a year, depending on the technique used.
The bodies are made of Japanese hard rubber (ebonite) in the studio. Ebonite is the perfect material for the production of stationery, very light and stable to alkalis, water and heat up to 150°C.
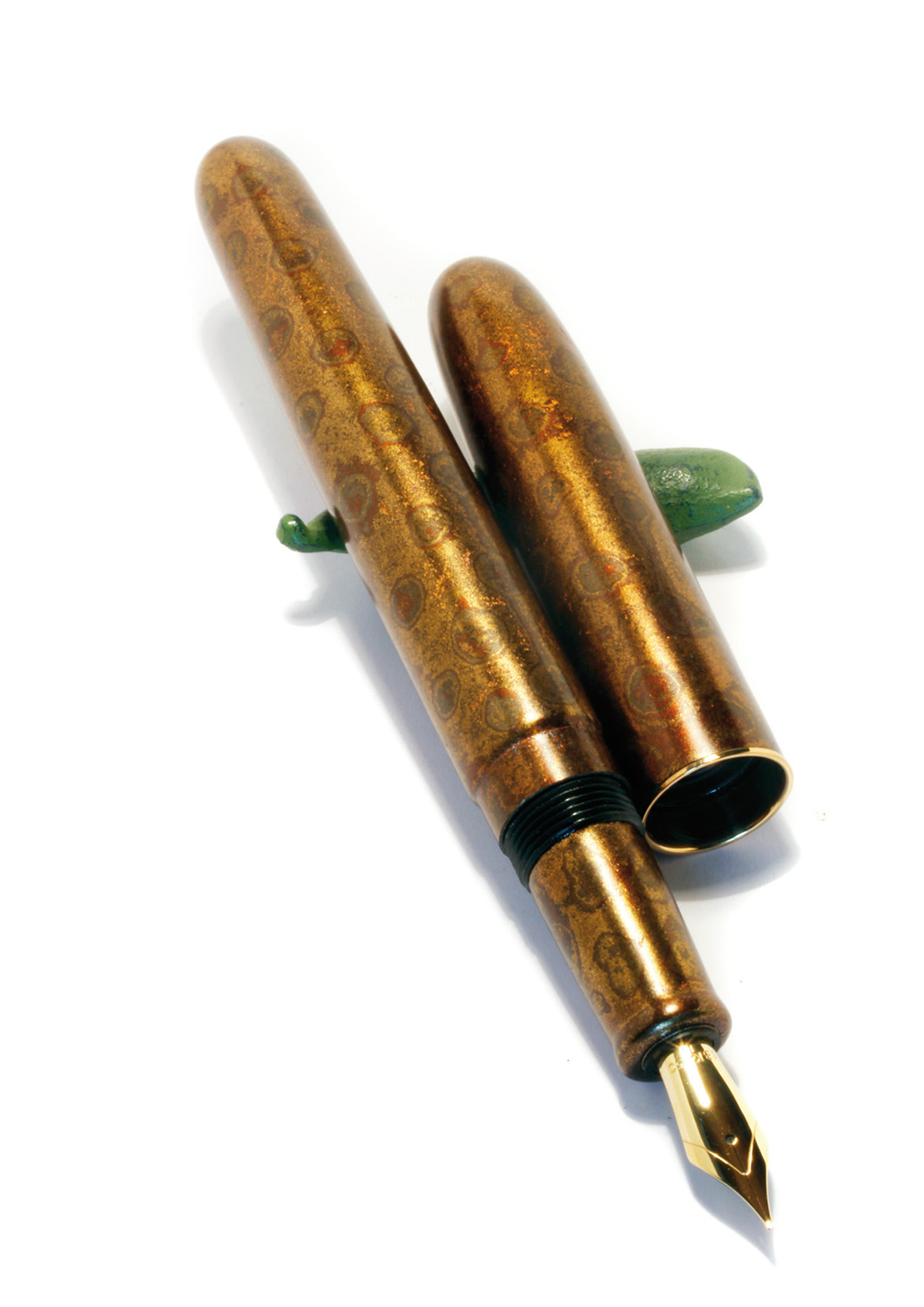
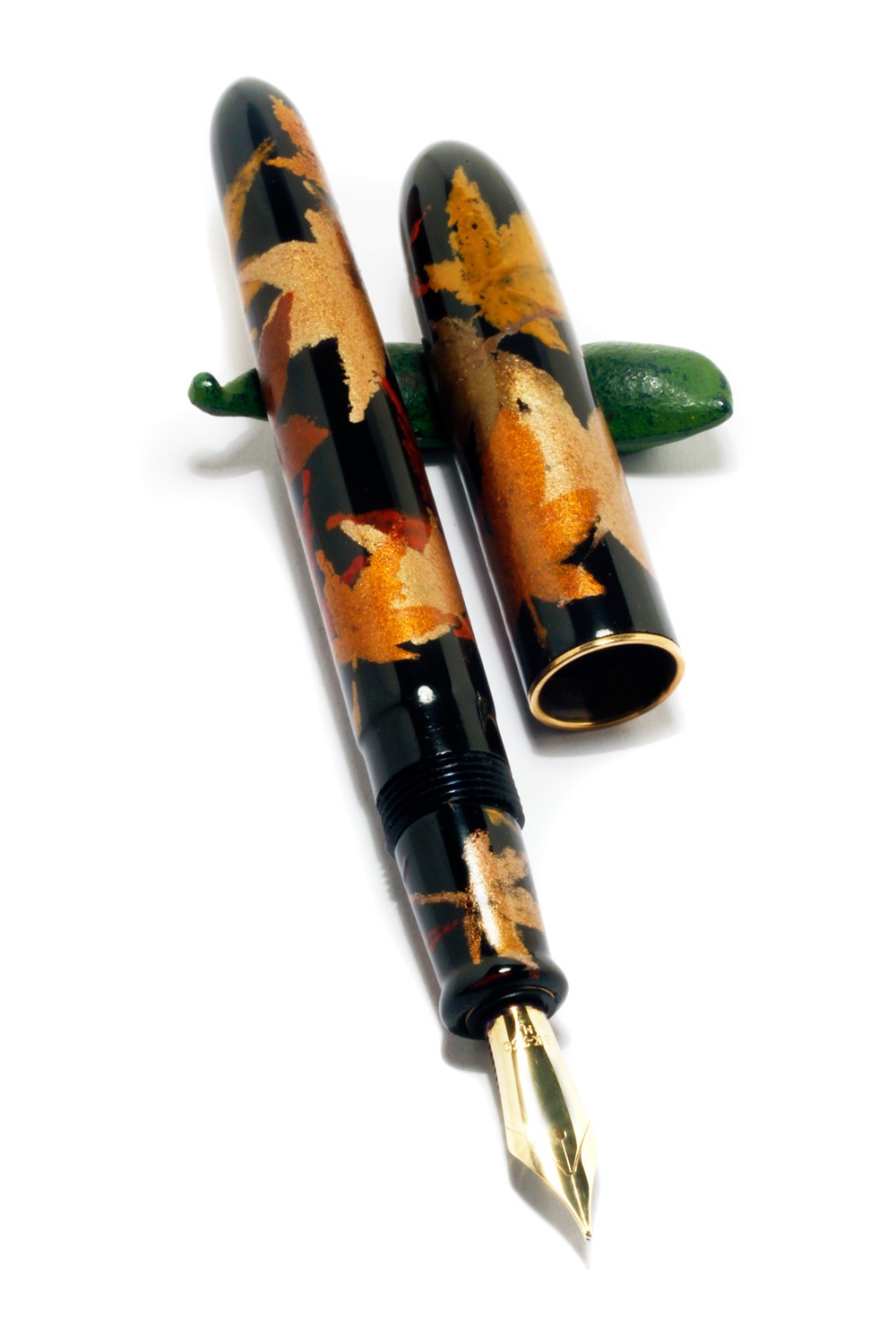
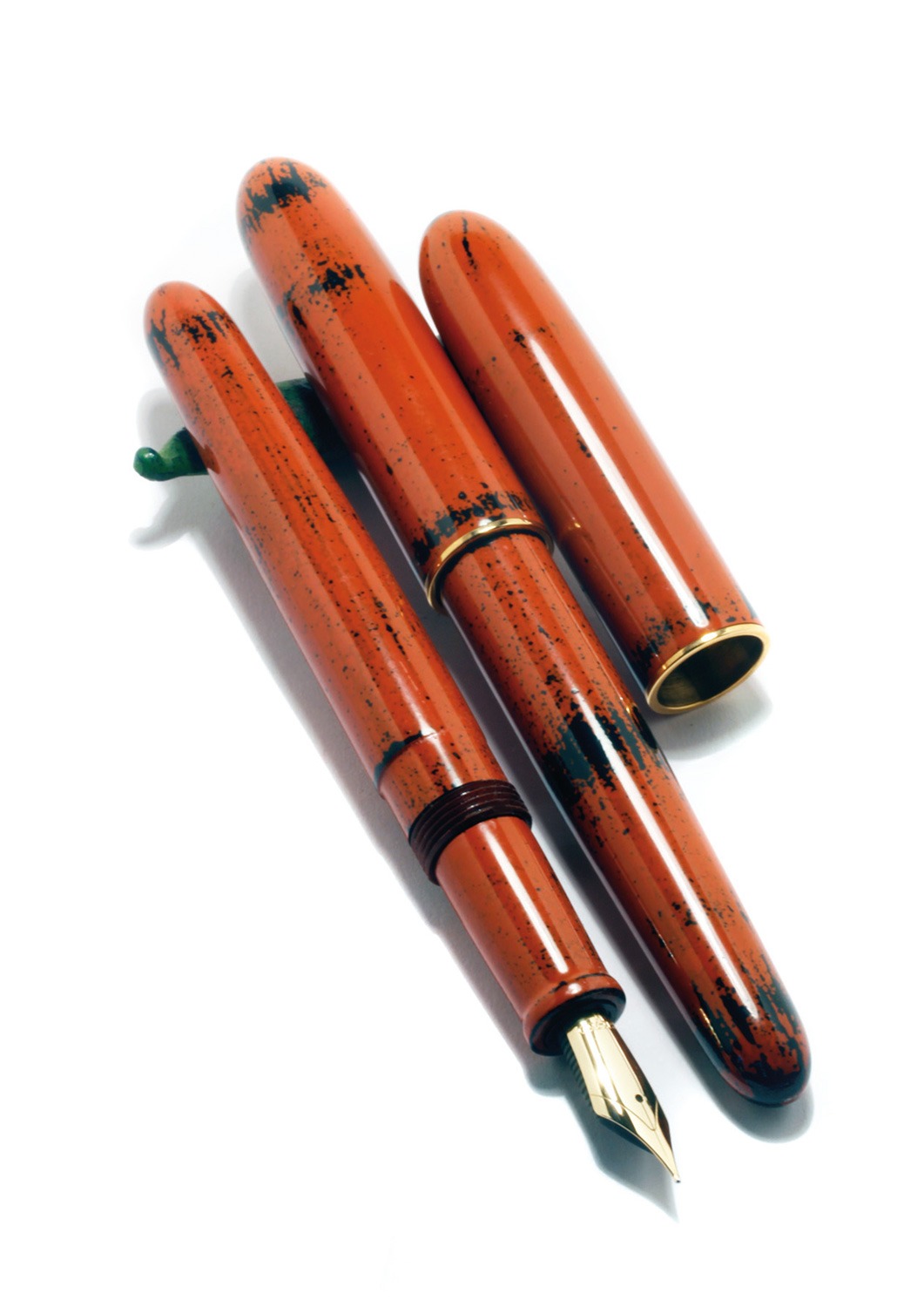
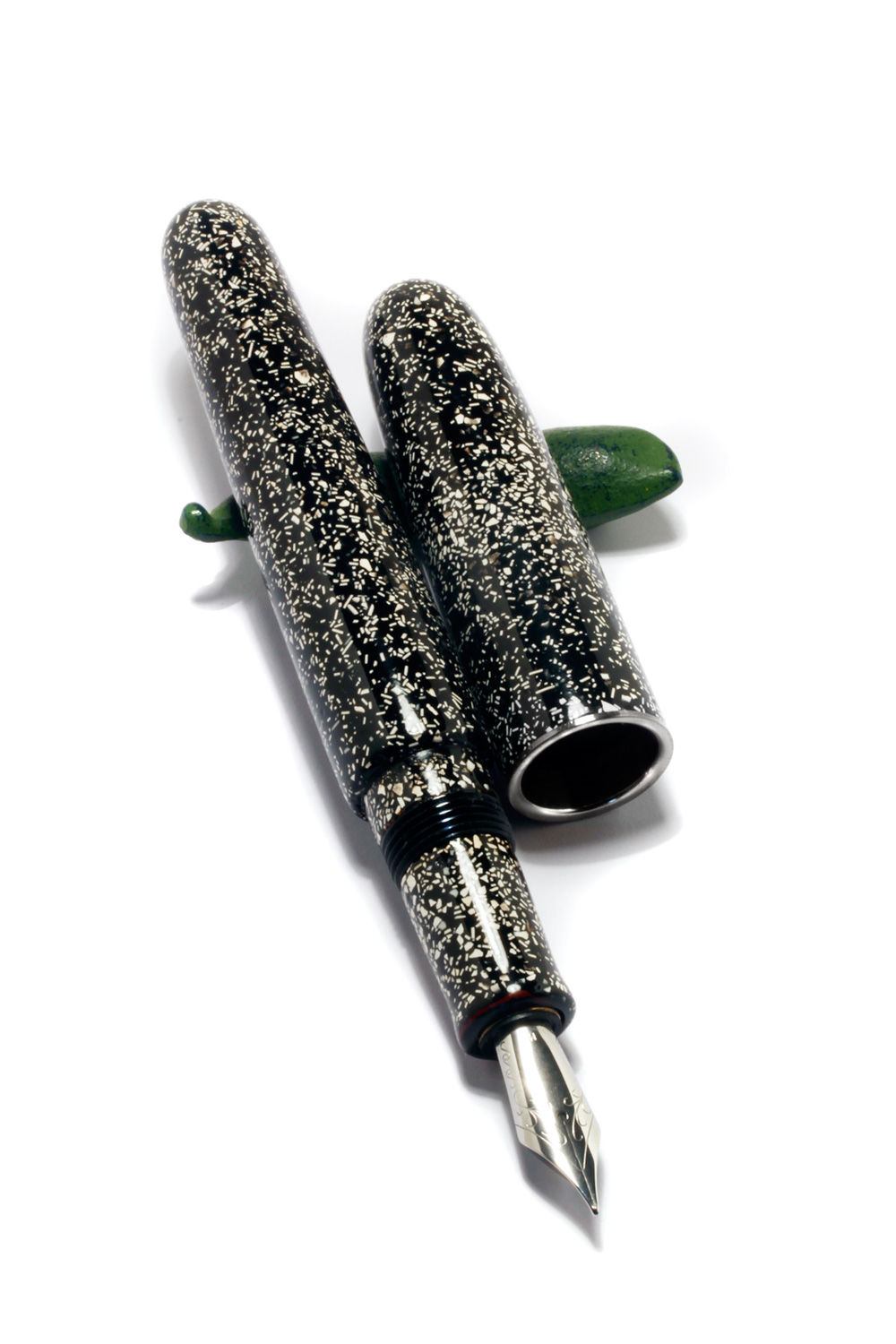
Manu Propria Pens
Pulverstrasse 8
3063 Ittigen-Bern
Switzerland
031 311 0011
- all photographs courtesy Manu Propria
Longing for knowing about urushi. Thank you